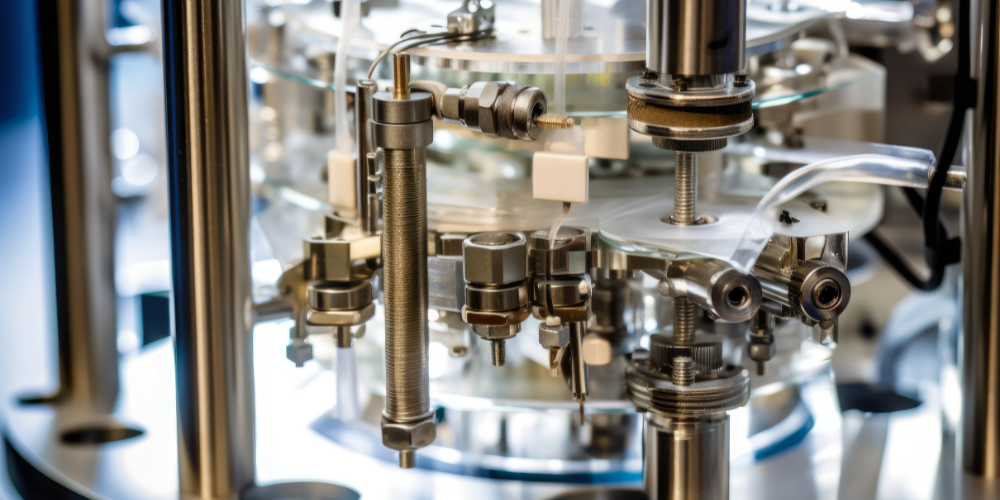
Qualified Bid: A "Qualified Bid" in procurement refers to a formal proposal submitted by a supplier or contractor that meets all the specified requirements, criteria, and standards outlined in a procurement solicitation or request for proposal (RFP). This
means that the bidder has successfully demonstrated their capability, competence, and compliance with the procurement's terms and conditions. Such bids are deemed eligible for further evaluation and consideration by the procuring entity.
Practical Example: Imagine a city government is soliciting bids for a construction project to build a new public library. A construction company submits a bid that not only includes the required documentation, such as financial statements and references but also showcases their relevant experience, proposed timeline, and a competitive cost estimate. This bid aligns perfectly with the city's specifications, making it a qualified bid eligible for review and potential selection.
Phonetic Notation: [kwol-uh-fahyd bid]
Qualify Control: Quality control (QC) is a fundamental component of the procurement process that focuses on ensuring that products or services purchased meet established quality standards and specifications. It involves a systematic approach to monitoring, inspecting, and testing goods or services during various stages of production, delivery, or implementation to verify their compliance with predefined quality criteria. Quality control aims to identify and rectify any deviations or defects to maintain consistent quality and minimize the risk of receiving subpar items. It helps organizations deliver products and services that meet or exceed customer expectations, enhance reliability, and reduce potential liabilities due to faulty or substandard goods.
Practical Example: In the automotive industry, quality control involves rigorous inspections and testing of components like engines, brakes, and safety systems to ensure they meet safety and performance standards. If a car manufacturer identifies a defect in the brake system during quality control checks, they will address and rectify the issue before the vehicle reaches the market, preventing potential accidents and ensuring customer satisfaction.
Phonetic Notation: [kwah-li-tee kuh n-trohl]
Qualitative: In the context of procurement and assessment, "qualitative" refers to the subjective evaluation or analysis of goods, services, or suppliers based on non-quantifiable characteristics, attributes, or factors. Qualitative assessments often involve considering qualities such as reputation, expertise, creativity, responsiveness, and overall fit with specific project requirements. These assessments are typically descriptive rather than numerical and can be used to make informed decisions when quantitative data alone may not provide a complete picture.
Practical Example: When a company is selecting a marketing agency through a procurement process, a qualitative evaluation might involve assessing the agency's past campaigns for creativity, the responsiveness of their account managers, and their understanding of the industry. These qualitative factors, in addition to quantitative metrics like cost, can help the company choose an agency that aligns with their branding and communication goals.
Phonetic Notation: [kwah-li-tay-tiv]
Qualitative Analysis: Qualitative analysis, within the realm of procurement and data assessment, refers to the process of examining and interpreting non-quantifiable information and attributes to make informed judgments or decisions. Unlike quantitative analysis, which deals with numerical data, qualitative analysis delves into subjective and descriptive aspects. It involves assessing factors such as quality, suitability, relevance, and the overall context of information to gain a deeper understanding of a situation. In procurement, qualitative analysis can be applied to supplier evaluations, risk assessments, and decision-making processes by considering factors like reputation, ethics, cultural alignment, and expertise.
Practical Example: Suppose a company is considering two potential suppliers for a critical component of their product. In a qualitative analysis, they may assess factors such as the supplier's track record for on-time deliveries, their willingness to collaborate on product improvements, and their reputation for customer service. This qualitative assessment, combined with quantitative data like pricing, helps the company choose the supplier that not only offers a competitive cost but also aligns with their strategic goals.
Phonetic Notation: [kwah-li-tay-tiv uh-nal-uh-sis]
Qualitative Measures: Qualitative measures, in the context of procurement and assessment, refer to non-numeric criteria and indicators used to evaluate the quality, characteristics, and attributes of products, services, or suppliers. These measures are typically descriptive and subjective, focusing on aspects such as reputation, expertise, responsiveness, and alignment with specific project requirements. Qualitative measures complement quantitative metrics and provide a holistic view for decision-makers, enabling them to make informed judgments beyond numerical data. In procurement, qualitative measures are essential for assessing factors like the suitability of suppliers for a project, their ethical practices, cultural compatibility, and overall fit with the organization's objectives.
Practical Example: When selecting a software development vendor, qualitative measures may include evaluating the vendor's past projects for innovation and creativity, assessing their communication skills and flexibility to adapt to changing project requirements, and considering client feedback on their responsiveness and problem-solving abilities. These qualitative measures help ensure the chosen vendor not only meets technical specifications but also aligns with the company's collaborative and innovative goals.
Phonetic Notation: [kwah-li-tay-tiv mezh-erz]
Qualitative Research: Qualitative research, in the realm of procurement and data analysis, is a systematic and exploratory method used to gather non-numeric data and insights related to human behavior, opinions, attitudes, and experiences. It involves techniques such as interviews, focus groups, observations, and content analysis to gain a deep understanding of qualitative factors that influence procurement decisions. In the procurement context, qualitative research can be employed to explore supplier relationships, assess supplier reputation, understand market dynamics, and identify factors that may not be easily quantifiable. It helps organizations make informed decisions by uncovering nuances and context that quantitative data alone cannot provide.
Practical Example: In a procurement scenario, a company conducting qualitative research might conduct interviews with key stakeholders to understand the subjective factors influencing their choice of suppliers. Through these interviews, they could uncover insights about supplier responsiveness, innovation, ethical practices, and cultural compatibility, all of which can inform supplier selection and relationship management.
Phonetic Notation: [kwah-li-tay-tiv ree-surch]
Fhyzics is an ASC of CIPS, UK and ACP of ASCM/APICS, USA offering procurement and supply chain certifications.
Quality Assurance (QA): Quality Assurance (QA) in procurement is a systematic approach to ensuring that products, services, or processes meet established quality standards and conform to specified requirements. It involves a comprehensive set of planned activities and processes designed to prevent defects, errors, or deviations from occurring during procurement, production, or project execution. QA encompasses quality planning, quality control, and continuous improvement to guarantee consistent and high-quality outcomes. In procurement, QA measures are applied to supplier selection, contract management, and product/service inspections to minimize risks, enhance product/service quality, and ultimately satisfy customer or stakeholder expectations.
Practical Example: Consider a manufacturing company that sources electronic components from various suppliers. To implement QA in procurement, the company may establish rigorous supplier qualification processes, conduct regular supplier audits, and perform product quality checks during the manufacturing process. By consistently monitoring and improving the quality of the sourced components, they can ensure that their final products meet high industry standards and customer expectations.
Phonetic Notation: [kwah-li-tee uh-shoor-uhns]
Quality Circles (QCs): Quality Circles (QCs) are small, voluntary groups of employees within an organization who come together to identify, analyze, and solve quality-related problems and improve processes in the workplace. These circles serve as a grassroots approach to quality management and continuous improvement. Members of Quality Circles typically work in the same or related areas and collaborate to address issues affecting product or service quality, productivity, and efficiency. The goal of Quality Circles is to harness the collective knowledge and experience of employees to implement innovative solutions, leading to enhanced product quality and overall organizational effectiveness.
Practical Example: In a manufacturing company, a Quality Circle might consist of assembly line workers who notice a recurring issue with a particular product's design causing frequent defects. They meet regularly, brainstorm ideas, analyze the problem, and propose design modifications. If their solution is approved and implemented, it can lead to a reduction in defects, improved product quality, and increased customer satisfaction.
Phonetic Notation: [kwah-li-tee sur-kuhls]
Quality Control: Quality Control (QC) is a systematic and integral part of the procurement and manufacturing process that ensures products or services meet specified quality standards and adhere to established criteria. It involves a set of processes, procedures, and techniques used to monitor and inspect various aspects of production or service delivery, aiming to identify and rectify any deviations or defects that may compromise quality. QC encompasses activities such as inspections, testing, documentation reviews, and process evaluations, with the ultimate goal of delivering consistent, reliable, and high-quality outcomes. In procurement, QC is vital for verifying that purchased goods or services conform to contractual requirements, industry standards, and customer expectations.
Practical Example: In the automotive industry, quality control is crucial during the assembly of vehicles. Workers on the production line perform inspections at various stages, checking for defects in components, paint quality, and overall assembly. If a vehicle fails QC checks, it undergoes necessary adjustments or repairs before it is approved for shipment, ensuring that customers receive automobiles that meet stringent safety and quality standards.
Phonetic Notation: [kwah-li-tee kuhn-trohl]
Quality Function Deployment (QFD): Quality Function Deployment (QFD) is a structured methodology used in procurement, product development, and project management to translate customer requirements and expectations into specific product or service features, attributes, and processes. It serves as a systematic approach to aligning customer needs with organizational capabilities, ensuring that the final output aligns closely with customer desires. QFD involves various tools and matrices that facilitate communication and collaboration among cross-functional teams, helping to prioritize and incorporate customer preferences into the design and procurement processes. By utilizing QFD, organizations can enhance product or service quality, reduce costs, and improve customer satisfaction through a data-driven and customer-centric approach.
Practical Example: In the development of a new smartphone, a company may use QFD to gather customer feedback and convert it into product features. For instance, if customers express a desire for longer battery life, the QFD process would guide the company to explore battery technologies, energy-efficient components, and software optimizations to meet this expectation effectively.
Phonetic Notation: [kwah-li-tee fuhngk-shuhn dih-ploy-muhnt]
Quality Inspection (Quality Control): Quality Inspection, often synonymous with Quality Control (QC), is a vital component of the procurement and manufacturing process aimed at ensuring that products or services meet established quality standards and adhere to predefined specifications. This process involves systematic and thorough examinations, assessments, and testing of goods or services at various stages of production, delivery, or implementation. The primary objective of quality inspection is to identify and rectify any deviations, defects, or discrepancies that could affect the final quality, safety, or functionality of the product or service. Quality inspectors employ a range of tools and techniques, including visual checks, measurements, and functional testing, to verify conformity to quality criteria.
Practical Example: In the food industry, quality inspection occurs at multiple stages. For instance, in a dairy processing plant, inspectors may examine milk samples for freshness and safety upon arrival. During processing, they can inspect equipment for cleanliness and functionality. Finally, before packaging, they might conduct sensory evaluations and lab tests to ensure the product meets taste, texture, and safety standards. Any deviations detected during these quality inspections are promptly addressed to guarantee product quality.
Phonetic Notation: [kwah-li-tee in-spek-shuhn (kwah-li-tee kuhn-trohl)]
Fhyzics offers the following procurement certifications:
Certified Professional in Sourcing Excellence (CPSE), IISCM, India
Certificate in Supply and Operations (Level 2), CIPS, UK
Advanced Certificate in Procurement and Supply Operations (Level 3), CIPS, UK
Diploma in Procurement and Supply (Level 4), CIPS, UK
Advanced Diploma in Procurement and Supply (Level 5), CIPS, UK
Professional Diploma in Procurement and Supply (Level 6), CIPS, UK
Quality Management System (QMS): A Quality Management System (QMS) is a structured framework, comprising policies, procedures, processes, and documentation, designed to ensure an organization consistently meets or exceeds quality standards and customer expectations in its products or services. It is a comprehensive approach to quality assurance and control throughout all phases of an organization's operations, from procurement and production to customer service and feedback. A well-implemented QMS encompasses aspects such as quality planning, quality control, quality assurance, and continuous improvement. It provides a systematic means to monitor, measure, and improve the effectiveness of an organization's processes, leading to enhanced product or service quality, increased customer satisfaction, and regulatory compliance.
Practical Example: In the pharmaceutical industry, a company may establish a QMS to ensure the quality and safety of its medicines. This system would include rigorous testing procedures, documentation of manufacturing processes, and regular audits to comply with strict regulatory standards. By maintaining a QMS, the company can confidently deliver safe and effective drugs to consumers.
Phonetic Notation: [kwah-li-tee man-ij-muhnt sis-tem (kyoo-em-es)]
Quality Register: A Quality Register is a structured document or database used in procurement and quality management to record and track quality-related information, data, and issues associated with products, services, or projects. It serves as a centralized repository for documenting quality objectives, standards, and performance metrics, as well as any deviations, non-conformities, or corrective actions taken to address quality issues. The Quality Register plays a crucial role in quality control and assurance, helping organizations monitor and manage the quality of deliverables and ensuring compliance with established quality criteria and requirements. It provides transparency, traceability, and a historical record of quality-related activities, which is valuable for audits, reviews, and continuous improvement efforts.
Practical Example: In a construction project, the Quality Register might include information about material specifications, construction standards, and quality expectations. If there is an issue with the concrete mix not meeting the specified strength, this deviation would be documented in the Quality Register, along with the corrective measures taken to rectify it, such as additional testing or replacement of materials.
Phonetic Notation: [kwah-li-tee rej-is-ter]
Quality Specifications: Quality Specifications refer to precise and detailed criteria, parameters, and requirements that define the acceptable quality and performance standards for products, services, or materials within the context of procurement and manufacturing. These specifications outline the essential characteristics, properties, and attributes that a supplier's deliverable must meet to fulfill contractual obligations and customer expectations. Quality specifications encompass factors such as dimensions, materials, tolerances, functionality, safety standards, and performance benchmarks. They serve as a critical reference point for both buyers and suppliers, ensuring a mutual understanding of what constitutes a satisfactory deliverable. Adherence to quality specifications is essential to guaranteeing product or service consistency, regulatory compliance, and customer satisfaction.
Practical Example: In the automotive industry, quality specifications for an engine component might include precise measurements, material composition, temperature tolerance, and performance parameters. For instance, a piston's quality specifications could specify its diameter, piston ring material, and heat resistance, ensuring that it functions effectively within the engine and meets safety and performance requirements.
Phonetic Notation: [kwah-li-tee spes-uh-fi-key-shuhns]
Quantitative: In the realm of procurement and data analysis, "quantitative" refers to the objective and measurable aspect of information or data. It involves the use of numerical values, statistics, and quantifiable measures to assess, analyze, or describe phenomena, making it possible to perform structured, systematic, and statistical analysis. Quantitative data provides a basis for making decisions, predictions, and comparisons with a high degree of precision and reliability. It contrasts with qualitative data, which deals with non-numeric attributes, descriptions, and subjective characteristics. In procurement, quantitative analysis can be applied to various aspects, such as cost analysis, supplier performance metrics, and demand forecasting, using numerical data to inform decision-making processes.
Practical Example: When assessing supplier performance, a quantitative approach might involve evaluating metrics like on-time delivery rates, defect rates per thousand units, or cost savings achieved through negotiation. These quantitative measures provide concrete data that can be used to objectively compare and rank suppliers based on their performance.
Phonetic Notation: [kwon-tuh-tay-tiv]
Fhyzics offers the following supply chain certifications:
Certified Inventory Optimization Professional (CIOP), IISCM, India
Certified Supply Chain Professional (CSCP) of APICS/ASCM, USA
Certified Planning and Inventory Management (CPIM) of APICS/ASCM, USA
Certified in Logistics, Transportation and Distribution (CPIM) of APICS/ASCM, USA
Certified in Transformation for Supply Chain (CTSC), IISCM, India
Quantitative Analysis: Quantitative analysis, in the context of procurement and data assessment, is a systematic and objective approach to examining numerical data to draw meaningful insights, make informed decisions, and identify patterns or trends. It involves the use of mathematical and statistical techniques to analyze quantifiable information, such as numerical measurements, financial data, or performance metrics. Quantitative analysis provides a structured framework for assessing and comparing data, enabling organizations to assess the effectiveness of procurement strategies, evaluate supplier performance, conduct cost-benefit analyses, and make data-driven decisions. It is a critical tool in procurement management, helping organizations optimize processes, reduce costs, and maximize the value of their procurement activities.
Practical Example: Suppose a company is considering two different suppliers for a key raw material. Quantitative analysis might involve comparing historical data on the quality, price, and delivery performance of each supplier over the past year. By applying statistical methods and financial metrics, the company can quantitatively assess which supplier offers the best overall value.
Phonetic Notation: [kwon-tuh-tay-tiv uh-nal-uh-sis]
Quantitative Measures: Quantitative measures, in the context of procurement and data analysis, refer to objective and numerical metrics used to evaluate and quantify various aspects of products, services, or processes. These measures involve the use of quantifiable data, such as numerical values, statistics, and performance indicators, to assess attributes, quality, efficiency, or effectiveness. Quantitative measures provide precise and objective information that can be used for decision-making, benchmarking, and performance evaluation. They are contrasted with qualitative measures, which deal with non-numeric attributes and subjective characteristics. In procurement, quantitative measures are instrumental in assessing supplier performance, cost analysis, demand forecasting, and risk assessment, offering a basis for making data-driven decisions.
Practical Example: In supplier performance evaluation, quantitative measures may include on-time delivery rates (e.g., 98% on-time deliveries), defect rates (e.g., 0.5% defect rate per thousand units), or cost savings achieved through negotiation (e.g., 15% cost reduction). These quantitative metrics provide clear and objective benchmarks for evaluating supplier performance.
Phonetic Notation: [kwon-tuh-tay-tiv mezh-erz]
Quantitative Research: Quantitative research, within the realm of procurement and data analysis, is a systematic and structured research method that relies on numerical data and statistical analysis to understand, measure, and draw conclusions about a specific phenomenon, situation, or set of variables. It involves the collection of data through structured surveys, experiments, or observations, where responses and observations are transformed into numerical values. These numeric data are then subjected to statistical analysis to identify patterns, relationships, and trends. Quantitative research is characterized by its objective and empirical nature, making it particularly useful for generating quantifiable insights and facilitating informed decision-making in procurement. It is often used for market research, supplier performance assessment, cost analysis, and demand forecasting.
Practical Example: In procurement, quantitative research could involve surveying a sample of customers to gather numerical data on their satisfaction with a supplier's products or services, using a scale from 1 to 5 to rate their level of satisfaction. The collected numeric data can be analyzed statistically to determine overall satisfaction levels and identify factors contributing to customer satisfaction or dissatisfaction.
Phonetic Notation: [kwon-tuh-tay-tiv ree-surch]
Quarantine Area: A Quarantine Area, in the context of procurement and supply chain management, is a designated and restricted space or location within a facility or a transport system where goods, materials, or products are isolated and held temporarily for inspection, testing, or other quality control measures. This area is used to separate items that may have been exposed to potential contamination, damage, or non-compliance with safety or quality standards. The purpose of a quarantine area is to prevent the release of potentially compromised or non-conforming goods into the regular supply chain until their quality, safety, or compliance can be verified. Items in quarantine are typically subject to thorough examination, testing, or evaluation before being released for distribution or use.
Practical Example: In a pharmaceutical manufacturing facility, a quarantine area may be used to isolate batches of medications suspected of contamination or quality issues. These medications are held separately while undergoing rigorous testing to ensure they meet safety and efficacy standards before being released for distribution to pharmacies and hospitals.
Phonetic Notation: [kwawr-uhn-teen eh-ree-uh]
Quota: A quota, in the context of procurement and international trade, refers to a government-imposed restriction or limit on the quantity of a specific product or category of goods that can be imported or exported during a defined period. Quotas are often used as a trade policy tool to regulate and control the flow of goods between countries. These limitations can be based on various factors, including national security, economic interests, or protection of domestic industries. Quotas can take the form of absolute quantity restrictions or percentage limits and may be allocated through various methods such as auction, historical entitlements, or first-come, first-served basis.
Practical Example: Suppose Country A imposes a quota on the import of foreign steel, limiting it to 100,000 metric tons annually. If businesses in Country A wish to import steel, they must ensure that the total imports do not exceed this predetermined quantity. Any steel imports exceeding this limit would be subject to penalties or rejected.
Phonetic Notation: [kwoh-tuh]
Quota System: A Quota System, in the context of procurement and international trade, is a government-established mechanism that places restrictions on the quantity or value of specific goods that can be imported or exported between countries during a specified period. It is a trade policy tool designed to manage and regulate trade flows, often with the goal of protecting domestic industries, ensuring national security, or balancing trade deficits. Quota systems can take various forms, including absolute quantity limits, tariff-rate quotas (TRQs) that combine tariffs and quantity limits, or preferential quotas that grant certain countries or entities preferential access to specific markets. These systems are typically administered by government agencies responsible for overseeing trade and customs.
Practical Example: Country X implements a quota system for the import of textiles, limiting the annual import of cotton fabric to 100,000 meters. Any business or individual looking to import cotton fabric must ensure they do not exceed this quantity. If the quota is reached, further imports are temporarily halted until the next quota period.
Phonetic Notation: [kwoh-tuh sis-tuhm]
Quotation: A Quotation, often referred to as a "quote," is a formal written document or communication provided by a seller or supplier to a prospective buyer or customer. It outlines the specific terms, conditions, and prices at which the seller is willing to supply goods or services. A quotation typically includes details such as itemized costs, quantities, delivery schedules, payment terms, and any other relevant terms and conditions. It serves as a critical part of the procurement process, enabling buyers to compare offers from multiple suppliers and make informed purchasing decisions. Quotations are legally binding when accepted by the buyer and form the basis of a contract between the parties.
Practical Example: A construction company seeking to purchase construction materials requests quotations from several suppliers. Each supplier provides a quotation specifying the quantity, quality, and price of the materials, along with delivery terms. The construction company reviews the quotations, selects the most favorable offer, and may enter into a contract with the chosen supplier based on the provided quotation.
Phonetic Notation: [kwoh-tey-shuhn]